Ebben az esettanulmányban megmutatjuk, hogy az AGCO, a világ egyik vezető mezőgazdasági gépgyártója hogyan használta a Visual Components-et összetett gyártóberendezések és munkafolyamatok digitális ikerként való modellezésére, melynek köszönhetően optimalizált gyártási cellákat tudott létrehozni, javítani tudta a gyártási folyamatokat és szimulálni tudta a bonyolultabb munkafolyamatokat.
Hogyan biztosíthatja a világ az élelmiszerellátást a jövőben a folyamatosan növekvő népesség számára? A mezőgazdasági ágazatnak egyre több gabonát, takarmánynövényeket és egyéb élelmiszertermékeket kell szállítania. Ezt pedig részben ellentmondó – költséghatékony, ugyanakkor környezet kímélő – célkitűzések mellett kell megtennie. Ezeket a célokat csak modern mezőgazdasági gépekkel lehet elérni, mert a pontos vetésnek, a célzott műtrágyázásnak és az optimális növényvédelemnek köszönhetően csak a modern technológia képes ésszerű költségekkel biztosítani a jó termést.
Az AGCO a világ egyik vezető traktor-, kombájn- és egyéb mezőgazdasági gépgyártója, amely olyan jól ismert márkanevek, mint a Fendt és a Massey Ferguson termékeit állítja elő. A bajor Asbach-Bäumenheimben található Fendt-üzem traktorokhoz, önjáró betakarító és növényvédő gépekhez gyárt vezetőfülkéket. Közel 1200 alkalmazott szerel, hegeszt, fest és különféle kialakítású kabinokat állít össze ebben a létesítményben. A traktorok összeszereléséhez a Fendt fülkéket Just-In-Time és Just-In-Sequence szállítják, vagyis az alkatrészek ugyanabban a sorrendben készülnek, mint ahogyan szükség van rájuk a közeli Marktoberdorfban található Fendt gyár futószalagján.
A vezetőfülke elengedhetetlen része egy hajlított és hegesztett csövekből álló szerkezet. A csöveket automatikusan szállítják egy tároló rendszerből és egy lézervágóba vezetik. Ezután továbbadják őket a hajlító gépeknek, ahol a be- és kipakolást robotok végzik automatikusan. A hegesztés előtti utolsó lépésként a csöveket 3D-s lézerrel vágják végleges kontúrjukra. Ez a művelet is automatikusan történik. Ezt követően a csöveket összehegesztik, hogy kialakítsák az utastér kereteket. Ehhez a legújabb hegesztési technológiákat és innovatív hegesztő robotokat használnak. A precíz vágásnak és a modern hegesztési folyamatoknak köszönhetően hajlított szélvédővel rendelkező ergonómikus kabinok készíthetők.
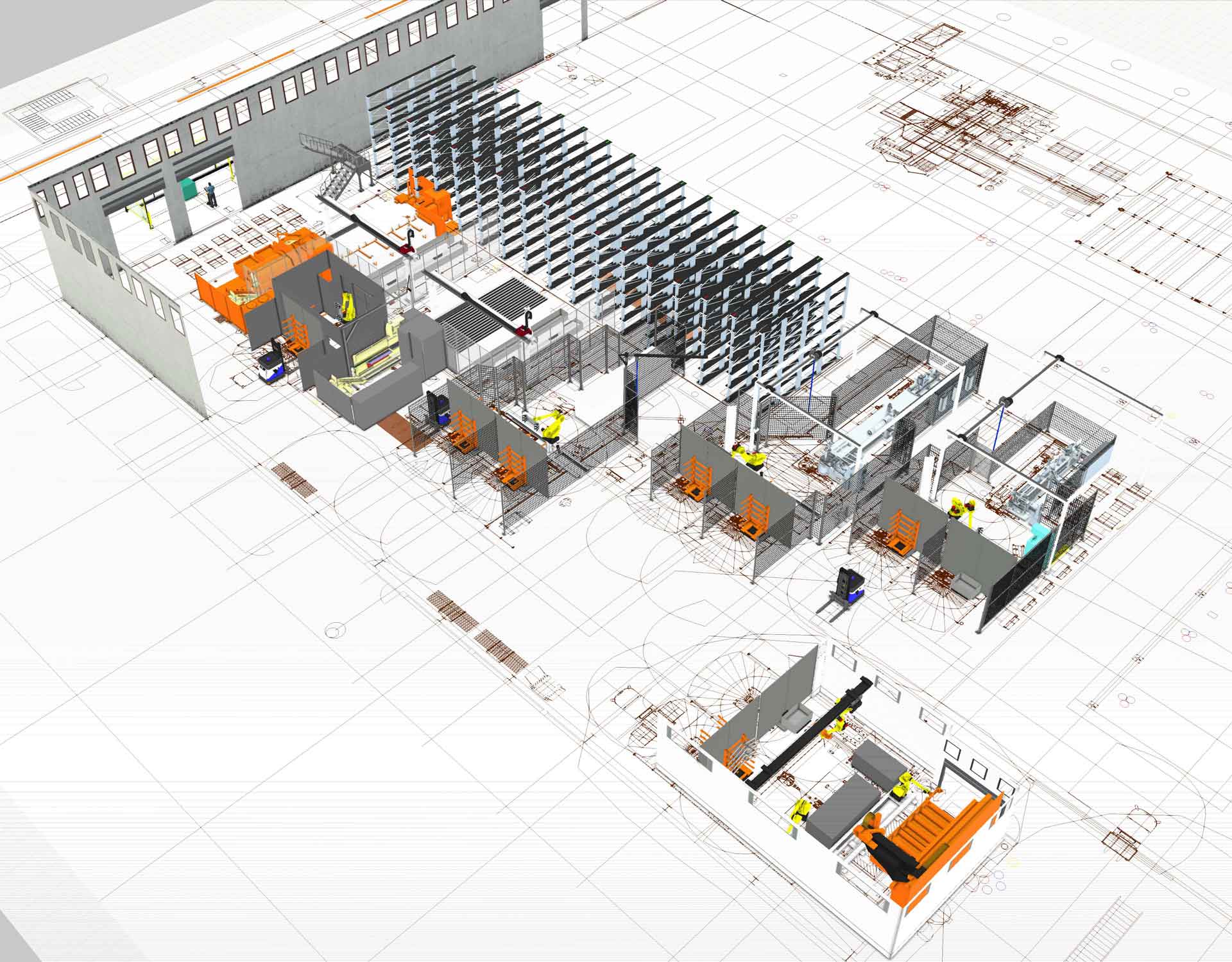
Az AGCO mérnöki osztálya felelős a folyamatok optimalizálásáért és a gyártóberendezések beszerzéséért. Optimalizálni szerették volna a robot szekvenciákat és fejleszteni az egyes cellákat a csőfeldolgozási munkafolyamatban. A csöveket összesen hat, egymással összekapcsolt rendszer dolgozza fel, nagyfokú automatizálással. Korábban az ilyen vizsgálatok elvégzéséhez és a lehetséges fejlesztések értékeléséhez le kellett állítani a gyártást, ami magas költségekkel járt. Ezért a mérnöki osztály jobb alternatívát keresett.
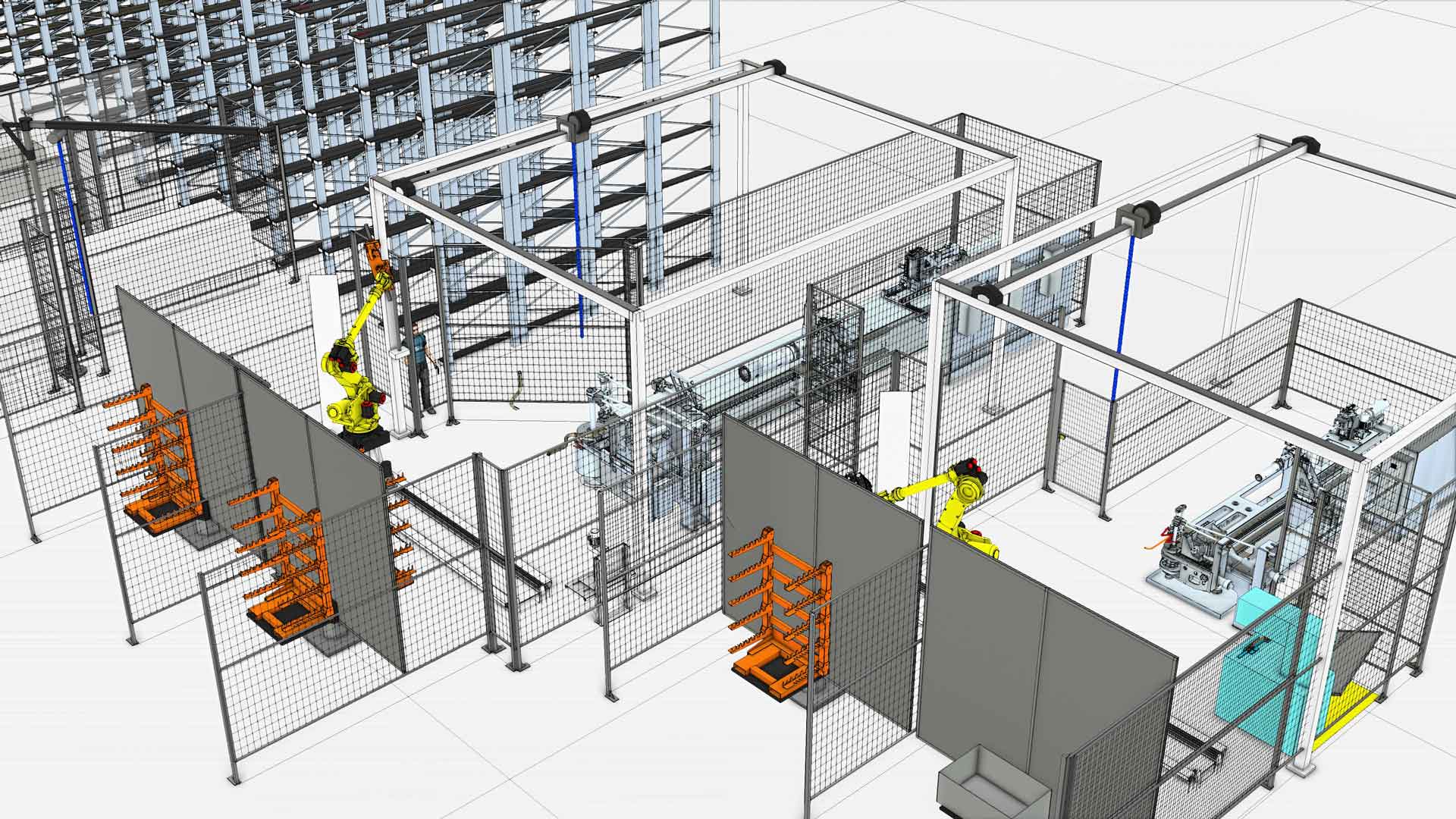
Úgy döntöttek, hogy a meglehetősen összetett gyártóberendezéseket és munkafolyamatokat digitális ikerként modellezik. A digitális iker javítja a folyamatokat, optimalizálja a gyártási cellákat és szimulálja a továbbfejlesztett munkafolyamatokat. A digitális iker alapot biztosít a jövőbeni optimalizálásokhoz is, arra az esetre, ha a robot további tevékenységeket végezne egy cellában.
Az AGCO mérnökei a finn Visual Components 3D gyár szimulációs szoftverben találtak rá a megoldásra. A Visual Components szimuláció felhasználható teljes gyártási rendszerek tervezésére és optimalizálására, ideértve a robotok offline programozását is. A szoftver a teljes gyártási folyamatot és a robotok, lézervágó és csőhajlító gépek közötti zökkenőmentes együttműködést szimulálja. A szimuláció lehetővé teszi a nem produktív idők minimalizálását és olyan kérdések megvizsgálását, mint a robot hozzáférhetősége és az ütközések elkerülése.
„Első lépésben nem volt fontos az összes rendszer minden részletében történő modellezése. Csak azok a gépek, amelyeket úgy gondoltunk, hogy módosítani kell. A szimuláció eredménye nagyon kielégítő volt. Például néhány berendezésen elérhetõségi vizsgálatokat végezhettünk, amelyeket korábban nem tudtunk volna megtenni a gyártás leállítása nélkül. És reálisan elemezni tudtuk a korábban csak becsülhető ciklusidőket”. – mondta el Norbert Pritzl, az AGCO projektfelelőse.
A projektet fokozatosan kibővítették, mivel az AGCO mérnökei egyre többet tudtak meg a Visual Components szoftver lehetőségeiről. Egy kis területtel kezdték, amelyet optimalizálni szerettek volna, majd a szimulációt fokozatosan kiterjesztették az egész automatizált berendezésre. A jövőben pedig a gyártás más területeit is optimalizálják a Visual Components szimulációs megoldásával.
Új szoftveres megoldás bevezetésekor általában elvárható, hogy a még ismeretlen eszköz kezelése bizonyos kihívást jelent. De ebben az esetben nem, mert a Visual Components-től kapott képzés és a jó kommunikáció sokat segített az alkalmazottaknak.
A Visual Components eCatalog-ja szintén rendkívül hasznos volt. A csőhajlítási, vágási és hegesztési folyamatban használt robotok és egyéb berendezések már elérhetőek voltak a könyvtárban. Ha az alkatrészek nem voltak elérhetők, azokat vagy rögtönözték, vagy egy CAD rendszerben modellezték, majd importálták a Visual Components programba. Itt nagyon hasznos, hogy a Visual Components-be számos CAD rendszerből tudunk modelleket importálni
„A Visual Components használatával olyan szimulációkat futtathatunk le gyártási folyamatunkról, amelyeket korábban csak a gyártás leállításával és a gyártósoron végzett kiterjedt teszteléssel lehetett megvalósítani” – mondja Pritzl, az AGCO munkatársa. „Ez lehetővé teszi számunkra az új koncepciók pontos modellezését és szimulálását is, hogy ezeket felhasználhassuk az árajánlatok bekéréséhez, például a berendezésgyártóktól. Ez rengeteg időt takarít meg a projektmenedzsmentben. A múltban sok helyszíni találkozóval, kidolgozott előadásokkal és részletes leírással közös konszenzusra kellett törekednünk. A Visual Components sokkal könnyebbé teszi számunkra a kommunikációt a nemzetközi berendezésgyártókkal”.
„A Visual Components használatával olyan szimulációkat futtathatunk le gyártási folyamatunkról, amelyeket korábban csak a gyártás leállításával és a gyártósoron végzett kiterjedt teszteléssel lehetett megvalósítani.”
Az AGCO munkatársa
A Visual Components lehetőségeivel kapcsolatos visszajelzések a vállalaton belül nagyon pozitívak voltak. A mérnöki osztály sok alkalmazottja várt ilyen eszközre. Ez nagy előnyt jelent a gyártóberendezések beszállítói számára is, mivel könnyebben megérthetik, hogy a kért berendezések mit csinálnak.
Az AGCO továbbra is használni fogja a Visual Components-et a jövőben? Norbert Pritzl-nek határozott elképzelései vannak erről. „A Visual Components-et más projektekben is felhasználjuk. Jelenleg olyan projekteken dolgozunk, mint egy új hegesztőcsarnok elrendezése és az összeszerelés optimalizálása. Most gyorsan és egyszerűen megjeleníthetjük és szimulálhatjuk az optimalizált koncepciót. Ez még több projekthez és ezáltal a termelés további optimalizálásához vezet”.
A gyártás korszerű automatizálása a legmagasabb szinten garantálja az egyes traktorfülkék tökéletes minőségét. A Visual Components megoldása nagy szerepet játszott abban, hogy versenyképes áron kiemelkedő minőségű kabinokat tudjunk gyártani traktorokhoz és egyéb mezőgazdasági gépekhez.