Az automatizálás virágkorában az ipari vállalatoknak azzal a kérdéssel kell szembenézniük, hogy miként használják fel az új technológiákat a vállalaton belüli információáramlás hatékony javítására. Főleg akkor lesz ez nagyon lényeges, amikor a vállalaton belül több IT rendszert működtetnek egymással párhuzamosan a különböző területeik támogatása érdekében, ami akadályozza a hatékony információcserét. Ennek következtében pedig hiba csúszik a gyártás irányításba is. A MES PHARIS – gyártás felügyelő, irányító rendszer ezekből a szituációkból menti ki a vállalatokat.
A következőben egy autóiparban tevékenykedő fröccsöntő és szerszámkészítő cég esete alapján bemutatásra kerül egy remek példa arra, hogy mennyire fontos a hatékony kommunikáció a vállalat üzleti, irányítási és gyártási területe között. A szóban forgó vállalat azért határozta el, hogy bevezeti a MES PHARIS rendszert, mert egyrészt érezhető problémái voltak a gyártástervezés során. Ezek a problémák pedig oda vezettek, hogy nem tudták időben teljesíteni a rendeléseiket, így kénytelenek voltak a szembenézni a késedelemért járó büntetéssel. Másrészt a cég tulajdonosa nem tudta felmérni milyen hatása van gépek mennyiségének és a foglalkoztatottságnak a növekedése a működés hatékonyságára, mivel eddig ezt nem tudták hatékonyan mérni. A MES rendszert viszont kifejezetten arra tervezték, hogy a gyártás állapotáról pontos információkkal lássa el a felsőbbrendű ERP rendszert, valamint egyértelműen meghatározza a források hatékonyságát.
A szóban forgó vállalat nagymértékben számítógépesített volt, vagyis működése során nagyjából 10 különböző rendszert használt (ERP, APS, CMMS, CAD/CAM, valamint ANDON és PDM megoldások), aminek következtében belső kommunikációja leginkább a gyerekek „süket telefonjára” emlékeztetett, ahol az adatok vagy elvesztek vagy teljesen eltorzultak. Ezért döntött úgy a cég, hogy lecseréli az önálló rendszereit egyetlen, moduláris MES PHARIS gyártás irányító rendszerre és ezt összeköti az ERP rendszerükkel is.
Az adatok összekötése a MES rendszer segítségével
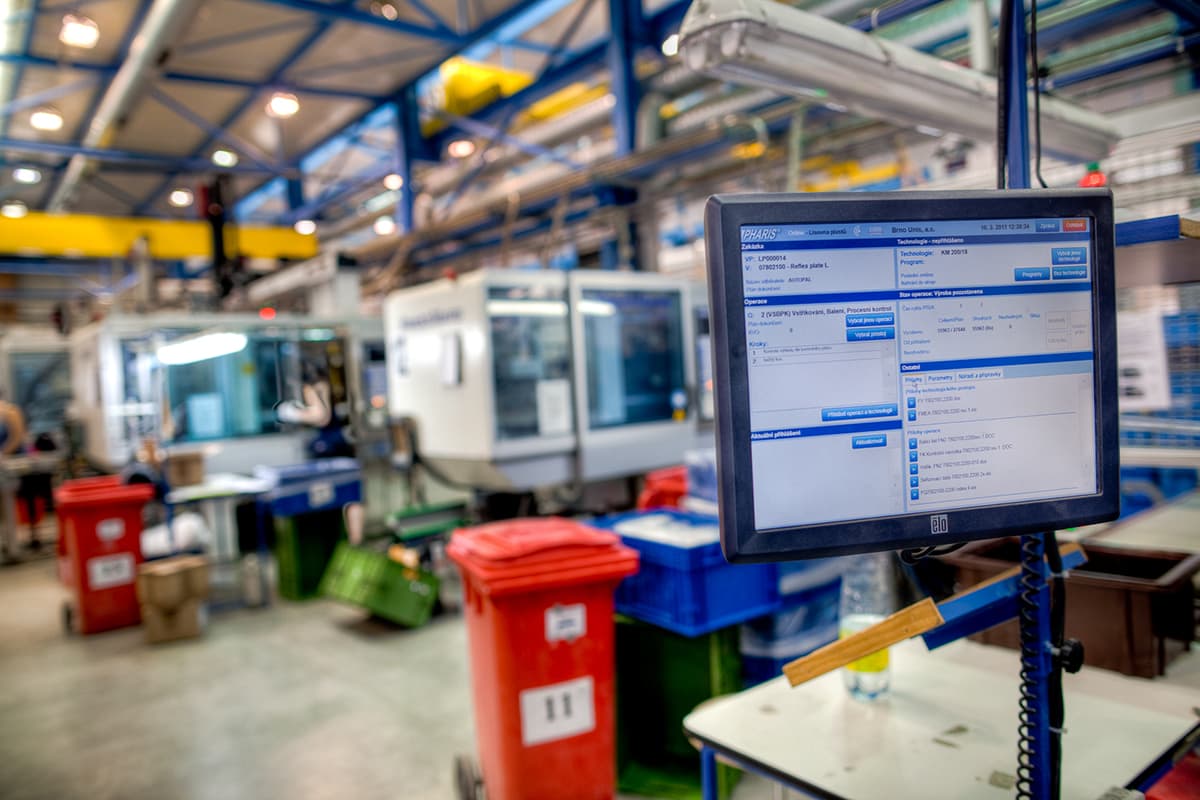
Kezdeti lépések
Az implementációs munka a gépek egyetlen hálózatba kötésével kezdődött. Ennek lényege, hogy a gépek állapotáról, a gyártott mennyiségről, a technológiai paraméterekről szóló információk automatikusan bekerülnek a MES PHARIS rendszerbe. A következő lépés során a legfontosabb gépek és gyártási területek mellé terminálokat kötöttek be, így a dolgozók be tudták táplálni a veszteségekről és az azok hatásairól szóló információkat. Így létrejött egy olyan munkarendszer, ahol a dolgozóknak lehetősége volt a többirányú ellenőrzésre – azaz a gépekből származó információ folyamatosan összehasonlíthatóvá vált a gépeket működtető emberek által betáplált információval. Valamint azokban az esetekben, ahol a visszautasított elemek száma meghaladta a beállított limitet, a rendszer automatikusan, egy előre beállított riasztási minta alapján, értesítette a gyártásért felelős dolgozót, aminek eredményeként csökkent a válaszadási idő és az anyagveszteség is.
Problémaelhárítás
Ezt követte a gépek technikai paramétereinek nyomon követése, ami egyrészt lehetőséget adott a hibák automatikus jelzésére és ezzel együtt a karbantartásért felelős személy riasztását, másrészt pontos adatokat szolgáltatott a hibákról, javításokról és az egyéb szolgáltatásokról. Ezen információk alapján pontosan kalkulálhatóvá vált az OEE, illetve lehetővé vált a gyors válaszadás minden, a gyártás során felmerülő probléma esetén.
Változás a gyártás tervezés területén
A korábban használt karbantartás támogató rendszert is lecserélték a CMMS MES PHARIS megoldásra így innentől kezdve az operátorok pontos információkat tudtak kinyerni a rendszerből mind a gépekre, mind a teljesített ciklusok számára vonatkozóan. A gyártás tervezés területén is változást hozott az APS MES PHARIS megoldás használata, mégpedig azáltal, hogy egy egységes környezetet alakított ki a gyártási folyamataik kezelésére. A tervezési modul rendkívül hasznosnak bizonyult és a MES rendszerrel összekötve itt is rendkívül gyorsan kezelhetővé tett minden, a gyártás során felmerülő eseményt. Az ütemtervek készítésekor a tervező azonnali visszajelzést kapott a be nem tervezett állóidőkről, az eszközök felülvizsgálatáról és karbantartásáról. Ezekből a virtuális forrásokból származó információkból a vállalat ki tudta következtetni, hogy az eszközökbe, munkaerőbe fektetett beruházás milyen módon fogja befolyásolni a gyártás hatékonyságát. A gyártási utasítások változásai szöveges üzenetként jelentek meg a gyártói paneleken és a dolgozó köteles volt elolvasni őket, majd az elektronikus aláírásával is megerősíteni azt. A már megemlített jótékony hatások mellett az is fontos, hogy az elektronikus dokumentáció bevezetése a vállalaton belüli munka is javult.
A változások hatása nem váratott magára sokat. Már 18 hónappal az implementáció első szakaszának végrehajtása után 18%-os növekedést tapasztalt a vállalat az OEE mértékében. Ezen túl a dolgozók barátságos munkatérben dolgoztak és a szerződés szerinti teljesítésben tapasztalható késedelmek is jelentős mértékben csökkentek. A változások továbbá nagy mennyiségű megtakarítást is eredményeztek, aminek köszönhetően nőtt a cég megbízhatósága és az ügyfeleik beléjük vetett bizalma is. A MES PHARIS rendszerbe való befektetés alátámasztotta a vállalat különböző területei közötti hatékony információ áramlás hatékonyságának fontosságát, valamint stabil fejlődést és mérhető profitot biztosított a vállalat számára.